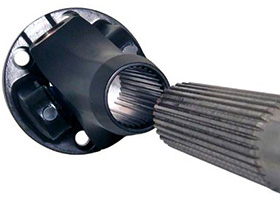
Кинематическое и силовое взаимодействие деталей и узлов в механизмах осуществляется посредством соединений различного конструктивного исполнения. В курсе деталей машин соединения классифицируются по нескольким признакам — по функциональному назначению, по целостности разъема, по подвижности составных частей, по форме и характеру сопряжения поверхностей соединения. Одним из достаточно распространенных в технике типов соединения является шлицевое, предназначенное для передачи осевого, вращательного движения или комбинированного их сочетания, относящееся к подвижным разъемным соединениям, также классифицируемое как один из типов зубчатых передач.
Шлицевое соединение, конструкция и назначение
Первые прообразы современной конструкции шлицевого соединения появились в винтовых механизмах времен Древних Египта и Греции. В привычном для нас виде они начали широко применяться в механике в период промышленной революции 18 века и с этого времени стали неотъемлемым и порою незаменимым элементом многих технических устройств.
Шлицевое соединение образуется двумя входящими в соприкосновение элементами — выполненными на валу зубьями и соответствующими им по форме впадинами (шлицами) на ответной ступице. Форма боковых поверхностей зубьев и впадин обеспечивает их плотное прилегание друг к другу, в зависимости от профиля зубьев различают соединения с прямобочными, эвольвентными и треугольными зубьями.
Прямобочные зубчатые соединения более просты в изготовлении и наиболее распространены, применяются при диаметрах вала до 125 мм. Эвольвентные обладают большей нагрузочной способностью, служат для передачи значительных усилий в узлах с диаметром вала до 500 мм.
Шлицевые соединения с треугольным профилем применяют для передачи небольших крутящих моментов или для точной регулировки взаимного расположения деталей в механизмах привода и управления. Число зубьев в соединении выбирается по допустимой нагрузке, в зависимости от которой различают лёгкую, среднюю и тяжелую серию соединения.
Областью применения шлицевых соединений является соединение валов между собой с помощью муфт, установка на валы различных деталей — зубчатых колес, шкивов, маховиков, фланцев, роликов, эксцентриков.
Достоинства шлицевого соединения
Шлицевое соединение условно можно представить в виде многошпоночного соединения, в котором шпонки выполнены заодно с валом. Близки эти два типа и по своему функциональному назначению, так что преимущества шлицевого соединения вполне целесообразно рассматривать именно в сравнении со шпоночным.
- За счёт большой площади контакта зубьев шлицевое соединение обладает высокой прочностью на смятие, срез, износ и допускает возможность передачи значительных крутящих моментов.
- Усталостная прочность и срок службы шлицевого вала в несколько раз выше, чем у вала такого же диаметра, ослабленного концентратором напряжения в виде шпоночного паза.
- В узлах с осевым перемещением деталей конструкция шлицевого соединения обеспечивает точную центровку сопрягаемых деталей и равномерность прилагаемого для перемещения усилия на всей длине зуба и ступицы.
- По сравнению со шпоночным соединением сечение шлицевого вала имеет больший момент инерции, что обеспечивает ему большую жесткость и большее значение сопротивления при изгибающих нагрузках.
- Шлицевое соединение позволяет передавать вращательное и осевое движение одновременно, без остановки механизма.
- Равномерность распределения нагрузки по зубьям обеспечивает высокую динамическую надежность шлицевого соединения в случае знакопеременных, переходных, в том числе реверсивных, с ударами и вибрацией режимов работы оборудования.
- При условии передачи одинакового крутящего момента габаритные размеры шлицевого соединения, в частности диаметр вала и длина ступицы, меньше, чем у шпоночного.
- По сравнению со шпоночным соединением шлицевое содержит меньшее количество деталей, что позволяет снизить трудоемкость при сборке и разборке механизма.
- Требования к типам, размерам и допускам шлицевых соединений устанавливаются государственными стандартами, что обеспечивает их унификацию и взаимозаменяемость при эксплуатации и техническом обслуживании оборудования.
Недостатки
Конструктивные особенности и определяемые ими условия работы шлицевого соединения вводят и ряд принципиальных, порою существенных, ограничений его применения в кинематических схемах.
- Для изготовления деталей требуется применение дорогостоящего специального оборудования, инструментов и оснастки.
- Для повышения прочности, твердости и износостойкости рабочих поверхностей может потребоваться дополнительная обработка зубьев — закалка, цементация, азотирование, также удорожающая стоимость изготовления.
- Трудоемкость и высокая стоимость изготовления деталей увеличивает стоимость узлов и механизмов в целом.
- При расчете зубчатого соединения следует учитывать неизбежную погрешность изготовления, приводящую к неравномерности распределения нагрузки между зубьями. Среднее значение поправочного коэффициента составляет 0,7-0,8, что довольно существенно снижает значение допустимого напряжения, увеличивает массу и габариты деталей.
- При использовании шлицевого соединения в составе высоконагруженных узлов и высокоскоростных передач (редукторы, коробки передач) требуется применение смазки.
- Применение шлицевого типа соединения ограничено условиями крупносерийного и массового производства.
- В отличие от шпоночного соединения, где в случае перегрузки происходит срез шпонки с ее последующей заменой, дефект или поломка одного из зубьев шлицевого соединения может привести к ремонту или замене вала и сопрягаемой детали.
Вывод
Совершенствование конструкции, технологии изготовления, повышение эксплуатационной надежности шлицевого типа соединения продолжается и в наши дни. Последним шагом стала разработка шарикового шлицевого соединения, обладающего более высокими показателями несущей способности и надежности.
По сложности и стоимости изготовления шариковые соединения пока уступают рассмотренным выше типам конструкции, но в ближайшем будущем вполне способны получить свое применение и составить достойную конкуренцию зубчатому типу шлицевых соединений.